在注塑加工工業(yè)的迅速發(fā)展的當(dāng)代,使人們對各種塑料制品的表面的質(zhì)量要求和尺寸的精度要求越來越高,尤其是在不同的工程技術(shù)中作為純粹的結(jié)構(gòu)零件使用的塑料制品,為滿足其使用的不同的物理性能和力學(xué)性能,主要的要求還是要制品組織致密、熔接牢固、強(qiáng)度高、內(nèi)應(yīng)力小。
With the rapid development of injection molding industry, people have higher and higher requirements for the surface quality and dimensional accuracy of various plastic products, especially the plastic products used as pure structural parts in different engineering technologies. In order to meet their different physical and mechanical properties, the main requirements are dense structure, firm fusion High strength and low internal stress.
但在注射模試模過程中,然后調(diào)整好注塑工藝的參數(shù)后,制品還常會出現(xiàn)填充不足、內(nèi)應(yīng)力高、表面流線等各種不同的現(xiàn)象,這主要原因是模具的排氣有問題。在模具進(jìn)行注塑加工的時候,模具內(nèi)產(chǎn)生的各種氣體主要有以下幾個來源和出處:有在型腔和澆注系統(tǒng)中存在的空氣;塑料原料中含有的水分在注射溫度下蒸發(fā)而成的水蒸氣;高溫下塑料分解所產(chǎn)生的氣體;
But in the process of injection mold testing, and then adjust the parameters of injection molding process, the products often appear various phenomena, such as insufficient filling, high internal stress and surface streamline, which is mainly due to the problem of the exhaust of the mold. During the injection molding process of the mold, various gases generated in the mold mainly come from the following sources: there is air in the mold cavity and gating system; Water vapor formed by evaporation of water contained in plastic raw materials at injection temperature; Gas produced by plastic decomposition at high temperature;
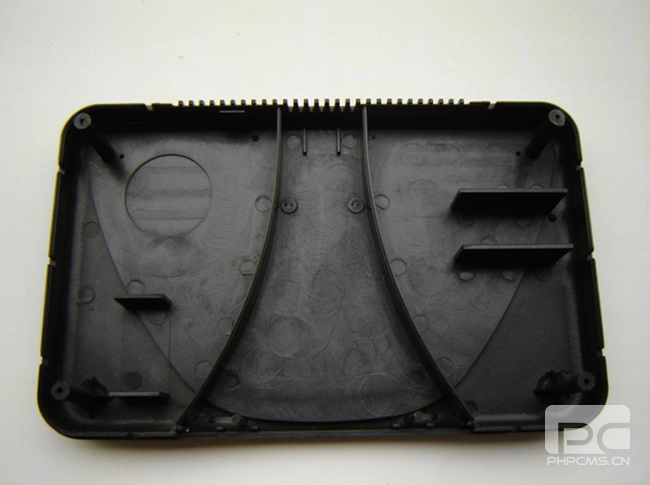
在注塑的時候塑料中一些添加劑揮發(fā)掉后或者一些熱固性塑料成形過程中交聯(lián)反應(yīng)所生成的氣體。同時在要保證注射成形的過程中要完整的脫模進(jìn)行,減少制品的成形缺陷,我們再考慮如何提高其質(zhì)量的注射加工工藝的同時,還必須重視其模具排出多余氣體的系統(tǒng)的設(shè)計。
During injection molding, the gas generated by cross-linking reaction after some additives in plastics volatilize or during the forming of thermosetting plastics. At the same time, in order to ensure the complete demoulding in the process of injection molding and reduce the forming defects of products, we must not only consider how to improve the injection processing technology of its quality, but also pay attention to the design of the system for discharging excess gas from its mold.
在注塑模具的過程中,如模具排氣不良,型腔中的氣體受到壓縮將產(chǎn)生很大的背壓,極大的阻礙了塑料熔體的正常快速充模,使注塑變得困難;同時會迫使注射時壓力不斷提高,保壓時間增加,成形周期延長,生產(chǎn)注塑件的時候效率也不停降低。有時候腐蝕性的氣體在型腔表面形成積垢,降低了模具正常使用下的壽命。
In the process of injection mold, if the mold exhaust is poor and the gas in the mold cavity is compressed, it will produce a great back pressure, which greatly hinders the normal and rapid filling of plastic melt and makes injection molding difficult; At the same time, it will force the continuous increase of pressure during injection, the increase of pressure holding time, the extension of forming cycle, and the continuous reduction of efficiency in the production of injection molded parts. Sometimes corrosive gas forms scale on the surface of the cavity, which reduces the service life of the die under normal use.
在注塑機(jī)塑料充模的過程中,為了將熔融的塑料的流動性保持在好的狀態(tài),因此必須要提高在熔融塑料的溫度和注射壓力,但也因為這樣制品的殘余應(yīng)力會隨之壓力而提高,產(chǎn)品四周的翹曲和塑料裂解的可能性也增加。
During the plastic filling process of the injection molding machine, in order to maintain the fluidity of the molten plastic in a good state, it is necessary to increase the temperature and injection pressure of the molten plastic, but also because the residual stress of the product will increase with the pressure, and the possibility of warpage and plastic cracking around the product will also increase.
比方模具的排氣正常情況下,注射速度可提高,充填和保壓可容易達(dá)到好的狀態(tài),不需額外增加料筒和噴嘴的溫度。這樣制品的殘余應(yīng)力小,翹曲變形小。注塑加工時候我們也要考慮如何排氣,好的排氣系統(tǒng)會提交塑料件的質(zhì)量。
For example, under normal conditions, the injection speed can be improved, and the filling and pressure holding can easily reach a good state without increasing the temperature of the barrel and nozzle. In this way, the residual stress of the product is small and the warpage deformation is small. During injection molding, we should also consider how to exhaust. A good exhaust system will submit the quality of plastic parts.